How Defoamers Improve Performance in Manufacturing and Production

Recognizing Defoamers
Defoamers play an essential function in numerous manufacturing procedures by properly combating the formation of foam, which can affect and interrupt procedures product high quality. Foam can emerge in numerous contexts, such as during mixing, home heating, or chain reactions, potentially causing inadequacies and inconsistencies in products. The system through which defoamers run usually includes lowering the surface area stress of the fluid, allowing bubbles to increase and coalesce to the surface a lot more conveniently, where they can after that break.
Reliable defoamers not only minimize foam development but likewise maintain compatibility with the product, ensuring that there are no damaging impacts on the last result. Comprehending the properties and features of defoamers is important for suppliers aiming to maximize their processes, boost efficiency, and maintain the stability of their products (defoamers).
Secret Advantages of Defoamers
Using defoamers in manufacturing processes provides a series of significant advantages that enhance operational effectiveness and product high quality. Among the primary benefits is the decrease of foam formation during manufacturing, which can obstruct equipment and interfere with process. By decreasing foam, defoamers guarantee smoother procedures, leading to reduced downtime and upkeep costs.
Furthermore, defoamers boost product consistency by protecting against air entrapment, which can compromise the stability of the end product. This is particularly essential in sectors where aesthetic appearance and structure are vital, such as in paints, layers, and foodstuff. Improved item top quality not just meets client assumptions yet also strengthens brand track record.
In addition, defoamers can assist in optimizing resource use. By enhancing the performance of resources application, they add to cost savings and decreased waste, lining up with sustainability goals. Finally, the application of defoamers can cause shorter processing times, allowing producers to boost manufacturing capability without considerable capital expense - defoamers.
Applications in Numerous Industries
In making procedures throughout numerous markets, the application of defoamers plays a critical role in boosting performance and item top quality. These chemical ingredients are utilized in markets such as food and beverage, pharmaceuticals, and fabrics to minimize foam-related difficulties.
In the food and beverage industry, defoamers are important during the fermentation procedure, avoiding foaming that can interfere with production and ruin the product's stability. Likewise, in the pharmaceutical sector, defoamers are utilized in the formula of liquid medicines, making sure harmony and stability while lessening waste.
Textile manufacturing also takes advantage of defoamers, as they are utilized in dyeing and finishing processes to promote also distribution more of dyes and chemicals. This application not just enhances the last item's appearance however also lowers the quantity of water and power taken in throughout production.
In addition, in the paper and pulp industry, defoamers aid preserve procedure efficiency by minimizing foam that can hinder machinery performance. Generally, the diverse applications of defoamers across these markets emphasize their significance in enhancing manufacturing processes and delivering premium products.
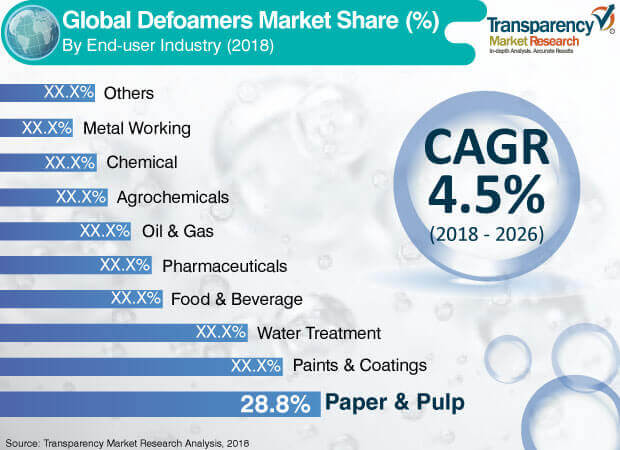
Selecting the Right Defoamer
Picking a proper defoamer is vital for maximizing performance and high quality in making processes. The choice of defoamer relies on different variables, consisting of the certain application, the kind of foam being generated, and the formulation of the item being manufactured.
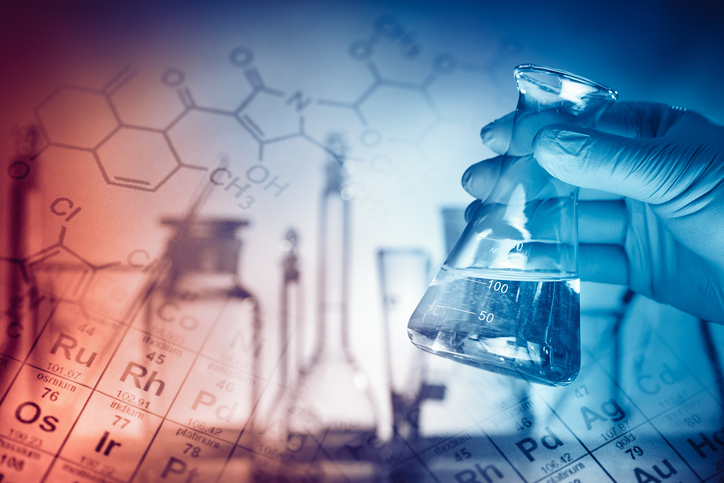
Firstly, take into consideration the chemical compatibility of the defoamer with other ingredients in your solution. A defoamer that interacts negatively with various other elements can adversely impact product top quality. In addition, Visit This Link the temperature level and pH array during handling are essential; some defoamers perform ideally under certain conditions while coming to be ineffective in others.
Second of all, examine the defoamer's efficiency features, such as its capability to promptly minimize foam and its persistence throughout production. It is necessary to pick a product that not only removes foam rapidly yet also maintains its effectiveness gradually.
Lastly, consider ecological and regulatory factors, specifically if your manufacturing procedure goes through stringent compliance requirements. Choosing a low-toxicity or eco-friendly defoamer can assist meet sustainability goals while making certain functional effectiveness. By attentively assessing these standards, suppliers can make educated decisions that enhance efficiency and item stability.
Best Practices for Implementation
Effective implementation of defoamers in manufacturing processes calls for cautious preparation and adherence to finest practices. Selecting the right defoamer, as previously gone over, is vital; guarantee it is compatible with the materials entailed and addresses the determined lathering concerns successfully.
Following, keep clear interaction with all stakeholders, including drivers and quality assurance teams. Educating sessions blog here can assist make sure that everyone understands the dosing procedures, possible influences on item high quality, and safety considerations. Executing a test phase can also be valuable; monitor performance carefully to assess effectiveness and make essential modifications.
Additionally, routine screening and surveillance of foam levels can give important understandings into the defoamer's performance over time. Changing does in response to adjustments in manufacturing variables will assist keep optimal efficiency - defoamers. Recording all processes and results advertises continuous improvement, permitting for fine-tuning of defoamer use and enhancing overall productivity in manufacturing operations.
Conclusion
In recap, defoamers play a crucial function in improving efficiency within manufacturing and production processes. By minimizing foam formation and helping with bubble coalescence, defoamers contribute to boosted product high quality, consistency, and operational efficiency.
The benefits prolong to product quality and price financial savings, as defoamers assist enhance processes.Defoamers play a vital duty in different manufacturing procedures by properly combating the formation of foam, which can affect and interrupt procedures product quality. Comprehending the homes and features of defoamers is essential for makers intending to optimize their procedures, enhance efficiency, and preserve the stability of their items.
Making use of defoamers in making processes supplies a range of substantial advantages that improve operational performance and product high quality.Additionally, defoamers boost product uniformity by preventing air entrapment, which can compromise the integrity of the final product.